Concrete Canvas Channel Lining at Avoca Mines
In 2017, Concrete Canvas was used to provide scour protection to drainage channels at the Avoca Mines in Wicklow. Find out how the project went below.
The location
Copper mining is reported to have begun in the Avoca River valley in 1720 and continued, intermittently, until 1982. Consistent mineral extraction has left an environmental legacy that comprises of open pits, shafts, spoil piles and former mining buildings.
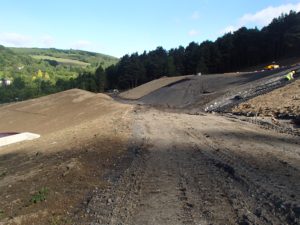
The project
During health and safety works that were being carried out by Civil and Environmental Engineering Contractor, Priority Construction Ltd., it was identified that the former mining site was impacting the quality of the water in the Avoca River. Water dischargers from abandoned copper and sulphur mines were acidic and metal laden, contaminating the nearby river water.
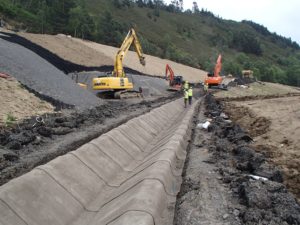
It was decided that the spoil areas would need to regraded and capped, with drainage channels to redirect upstream drainage around the site, instead of through it. Whilst the original design used a combination of precast concrete channels and HDPE liner, there were concerns around the long lead in times for the precast concrete and the construction risks associated with steep slopes. Instead, Priority Construction Ltd. proposed the use of Concrete Canvas.
The solution
At Concrete Canvas, we offer Geosynthetic Cementitious Composite Mats (GCCMs), which are an alternative to traditional concrete methods. Unlike most concretes, our GCCM uses a specialist high early strength concrete, with a limited alkaline reserve. This means it has a very low wash out rate and can be directly discharged into the water course, without the need for prior treatment, making it an ideal solution for channel lining.
For this project, we recommended the use of CC13™, which is our thickest type of GCCM. However, before the installation process could begin, the channel needed to be excavated and compacted to profile. A 250mm x 250mm anchor trench was then built on either side of the channel to allow the leading edge of the GCCM to be buried, preventing any undermining. Once the channel was prepared, the CC13™ was mounted onto a spreader beam and hung from an excavator, allowing it to be easily unrolled. Each piece of CC13™ was cut to a specific profile length and dragged into place, minimising material waste.
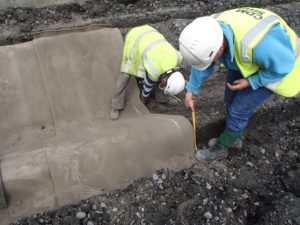
Priority Construction Ltd. installed the CC13™ transversely to accommodate for change in the channel profile, with layers overlapping by 100m in the direction of the water flow. The overlaps were then sealed using Everbuild Clearfix adhesive sealant and screwed together using stainless steel screws. As an extra precaution against undermining, 250mm steel ground pegs were also inserted into each overlap in the anchor trenches and then backfilled with material.
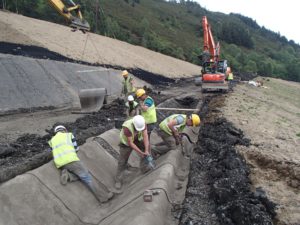
As the channel was located on a steep hill, concrete steps were installed to dissipate the water energy. Due to the flexibility of CC13™, it was able to be laid over each step and pinned into the vertical interface of the steps using Hilti anchors. After each day of work, the CC material was hydrated using a hose and a 6000ltr water carrier.
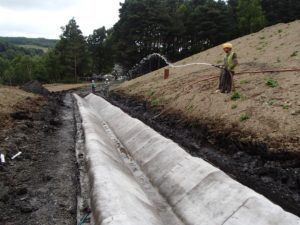
The results
In total, 1,520m² of CC13™ was installed within two weeks, providing long-term scour protection and erosion control for the network of drainage channels on the site. Despite the steep and varying slopes, we achieved installation rates of over 200m² per day.
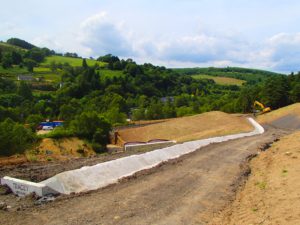
Following the success of this installation, Concrete Canvas is now being considered for multiple projects in the same region, in both the public and private sectors.
“After carrying out some research into alternatives for in-situ or precast concrete drainage channel we encountered Concrete Canvas. As we learned more about this solution we realised it would be ideal for the Avoca Mines Remediation Project which we had been awarded. We succeeded in gaining approval from the client for the use of Concrete Canvas. As the project progressed it became clear that this solution provided a number of benefits when compared with traditional methods. These benefits included speed of installation and flexibility in terms of levels e.g. where there were changes in design levels. I intend to use this product on future projects where possible.”
Ken Madden – Senior Contracts Manager, Priority Construction Ltd.
Contact Concrete Canvas for Channel Lining
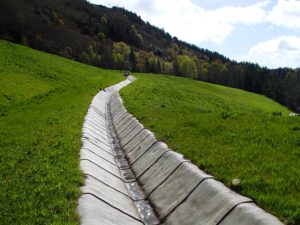
If you are looking for a flexible and durable concrete solution for your channel lining project, get in touch with Concrete Canvas. We can assess your project requirements to match you with the most suitable type of GCCM. With no need for plant or mixing equipment, we can even guide you through the installation process: simply unroll, secure and add water.
Get in touch